GHG emissions reduction in operations
In 2019, carbon dioxide (CO2), methane (CH4), and nitrous oxide (N2O) emissions levels directly related to our operations (Scope 1) totaled 10.6 mn t CO2 equivalent (2018: 11.1 mn t CO2 equivalent). The other GHGs are not relevant to our business and therefore have not been included in our figures.
Scope 1 emissions
In 2019, we continued implementing greenhouse gas reduction projects with an annual reduction of around 154.5 kt CO2 equivalent. All GHG reduction projects implemented in our operating countries between 2009 and 2019 have delivered a total reduction of 1.8 mn t CO2 equivalent to date. Reduction of carbon intensity in operations is mainly due to the implementation of projects directed at the reduction of flaring and venting.
Routine flaring reduction efforts
Phasing out routine flaring is one of the essential steps toward combining resource efficiency with long-term economic success and a way to strongly support our efforts to reduce the carbon footprint of our operations. In 2019, OMV routine flaring was 501.4 mn m3. In 2017, to reinforce our clear commitment to responsible resource management and sustainable business, we also endorsed the World Bank’s “Zero routine flaring by 2030” initiative to end the routine flaring of associated gas during oil production by 2030. We report annually to the World Bank on our progress in adherence to this initiative.
New OMV oil and gas fields are developed and operated according to plans that incorporate sustainable utilization or conservation of the field’s associated gas without routine flaring. Existing sites where routine flaring of associated and free gas still takes place are required to develop a phase-out plan to eliminate legacy routine flaring as soon as possible, but no later than 2030.
Many activities and projects to stop or reduce routine flaring have already been implemented or are ongoing, such as the Energy Efficiency Program in OMV Petrom Upstream. All OMV operations are required to minimize methane emissions from point sources as well as fugitive emissions and technically unavoidable emissions (such as well testing and well workover, among others). The main sources of methane emissions are routine/non-routine venting of gas during oil and gas production and processing as well as gas leaks.
Sustainability Strategy 2025 target
Achieve zero routine flaring and venting of associated gas by 2030
Status 2019
- The amount of hydrocarbons flared or vented in Upstream has been reduced by 37% vs. 2010.
Action plan to achieve the target
- Prepare and approve routine flaring phase-out plans
- Continue with ongoing flaring and venting reduction projects
- Systematically monitor and report on GHG performance
- Report our progress on routine flaring phase-out in conjunction with OMV’s commitment to the World Bank
- Main projects contributing to this target will be effective 2020 onward.
Methane emissions are monitored or estimated and controlled systematically by leak detection and repair programs. The identification of methane emissions sources serves as the basis for developing methane reduction projects in accordance with best practice in the industry and the best available technologies. Knowing the main potential sources of methane emissions also allows us to implement precautionary measures for preventing such emissions in new production assets.
Methane emissions
In kt
The minimum requirement for identifying leaks is conducting routine audio, visual, and olfactory inspections as part of daily operator rounds at all relevant OMV operating facilities. Leak detection also entails soap-bubble testing and optical gas imaging with defined scopes and intervals (annually or more frequently, as required in accordance with a related risk assessment). At some facilities, infrared cameras are also used for leak detection.
GHG emissions reduction in Upstream and in refineries
We implemented various activities in our Upstream and Downstream Business Segments directed at reducing GHG emissions. For example, significant reduction of venting and fugitive methane emissions is achieved in the OMV Petrom Upstream business thanks to modernization of transportation infrastructure, replacement, and optimization, which led to a significant reduction of accidental venting and also to the reduction of gas consumption (e.g., Merişani and Vâlcele compressor stations in the Muntenia Vest asset, gas networks monitoring in the Moesia asset, new production facilities in Mădulari in the Oltenia asset, improved gas pipelines infrastructure in the Crișana Banat and Muntenia Vest assets).
In refineries, optimal plant design is implemented in order to minimize flaring events by balancing the fuel gas system. Such advanced process control includes sufficient capacity of the flare gas recovery system, the use of high-integrity relief valves, and other economically viable organizational and control measures. As a result of such measures, we aim to use flaring as a safety system for other than normal operations, such as start-up, shutdown, emergency, process upsets, and others.
Upstream – gas treatment plant at Hurezani
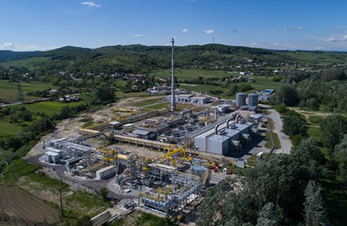
Between 2010 and 2019, Upstream developed a centralized gas treatment hub in the Oltenia asset to serve domestic gas production in south-eastern Romania. The latest stage of the project started in 2017, amounted to EUR 50 mn, focused on the development of a new efficient gas treatment process – Centralized Hydrocarbon Dewpoint (CHD) Hurezani –, and also addressed the modernization of Compressor Station Hurezani Area 2. The project features the installation of gas treatment units and pipeline infrastructure, thus completing the overall gas compression and treatment chain. The facilities modernized in 2019 increase energy efficiency and reduce GHG emissions by around 9,230 t of CO2 equivalent per year.